The Portuguese language received an award from Coldwell Banker for leadership.

This interview was first published in the September issue of TRAÇO architecture magazine.
Where did this respect for the use of wood in your projects come from? Today, there is a lot of talk about sustainability and, in fact, wood is one of the most interesting and important renewable materials. In Portugal, there has always been a certain prejudice against the use of wood due to thermal variations and maintenance. Although, in my opinion, this is often not related to the use of wood, but to its improper use. That is why I started investing early in studying wooden construction. We completed the project Pedras Salgadas with eco-houses and snails. We also used a lot of cryptomeria in the project in Longrove. We have experience in this field. Recently, we built a house, which, for a number of reasons, including project analysis, programs, site, and location, is, if not the first, then one of the first projects in Portugal to use CLT.
Are you talking about the "Casa3000" project?
"Casa3000" is a project that arose from circumstances. There were few people willing to work on the construction site, the house was completely removed from the city limits, there were problems with electricity and water supply, the nearest power point was2 km away from the house, and all these circumstances led us to create a house that is completely self-sufficient in terms of energy. Although, of course, there is no such thing as a100% self-sufficient house, there will always be a small generator for special cases. And we decided to build it out of CLT.
Was it an easy decision?
I have always advocated for this technology, and time has proven me right. Back then, it was little known in Portugal, and when I talked about it with a construction engineer, it felt like I was taking food out of his mouth because he didn't know how to make the calculations. If I spoke with a contractor, he dismissed this solution because he made very simple cost comparisons. In other words, if you only compare the cost of CLT with a more traditional material, it might seem more expensive. But that's not the real issue.
Responsibility of architecture
And what is this problem? Building with CLT allows for many things. First of all, it is dry construction, which significantly reduces the number of operations on the construction site. The panels are already cut, and every millimeter is precise. This is a precise and very efficient assembly with a small number of workers on site. Today, there is a serious problem in Portugal with hiring specialists not only in construction. CLT is a technology that aligns with modern times, as it allows for a significant increase in the volume of prefabrication on site, better cost control, and better results in terms of construction costs and timelines. It has a number of additional advantages. For example, fire safety is often discussed, and in this regard, CLT is also advantageous because it is glued wood that does not burn but carbonizes, significantly reducing the risk of ignition. It also greatly enhances the seismic safety of the building because, as we know, this material is very flexible and has better strength. In terms of comfort, wood improves acoustic and thermal comfort. I believe that construction in Portugal will move towards prefabrication; it is inevitable. And if the Portuguese do not understand this now, they will realize it in some time when the war in Ukraine ends and reconstruction begins. Then we will witness the relocation of workers and construction companies.
But don't you feel that there is now a greater use of CLT and prefabrication in construction overall?
Undoubtedly. Today, companies are beginning to realize the advantages, study, and engage in this process. A number of engineers are currently being trained to conduct calculations, which is fundamental, as it is known that wooden construction does not allow for large inertia coefficients. I am convinced that the trend is moving towards prefabrication, whether using CLT or other technologies; there are over 100 different prefabrication technologies in the world. This is a path that will continue in Portugal, and architects will have to get used to it because they will need to learn to work with other materials and solutions, not just concrete and brick.
Is training a concern in your workshop?
Of course! We have been concerned about this for a long time.
Return to CLT
In your current projects, are you using CLT again? We are currently at a stage where it is still difficult to convince our clients and promoters that CLT is a good solution, but we are confident that within the next two to three years, we will have built thousands of square meters using this technology. I have no doubt that we are preparing several projects in this area. It all started with the "Casa 3000" project.
Would you change anything about what you did in your first experience working with CLT?
I wouldn't change anything. This is a project that we are very proud of in the workshop, just like all our projects. We don't look back; we look forward. Our passion is the next project we will have; the others remain in history. We strive to execute all projects at the highest level, but sometimes some of them turn out differently than we wanted. However, I have the opportunity to correct that. We care deeply about not being ashamed of what we place in the landscape. I usually say that we, as architects, are the Guardians of the Landscape. We don't have one client; we have several clients. We are invited by a client who pays us, we are monitored by the municipality, often poorly, due to the ignorance of their own technical specialists who are afraid to evaluate the project and support good projects because of their lack of knowledge, and we have another client who is the invisible client - all the people who have to live with what we create and build in the landscape. Therefore, for me, the greatest rewards are the people who approach me on the street to thank me because the neighborhood has changed [in the context of the Casa das Fragâncias project on Rua do Patrosínio] or in Pedras Salgadas, where we were able to bring life back to that area. These are the great rewards for us; they make our profession a Great Profession.
Does the use of CLT or wood in general change the way architecture is created?
The tree has become the raw material we work with, and it doesn't limit our creativity. We don't feel constrained by the fact that we are drawing from a material that seems very rigid. It's part of the analysis, part of the process. In all the projects we work on, there is a strong rationale. Nothing happens by chance. In "Casa 3000," which may seem like a joke, nothing there happened by accident. I have a great distrust of engineering projects today because engineers do everything by the book and don't look at the DNA of things like we architects do. And when it came to a house made entirely of CLT and fully self-sufficient, my first concern was to talk to the University of Aveiro to have them oversee all the specialized projects to ensure that what was being designed was indeed correct and functional. We very often seek support from universities to make sure that what we are doing is done right.
Today, there is a lot of talk about sustainability, but then we see buildings made of glass. Recently, I was in Aveiro and
Comment
Popular Posts
Popular Offers
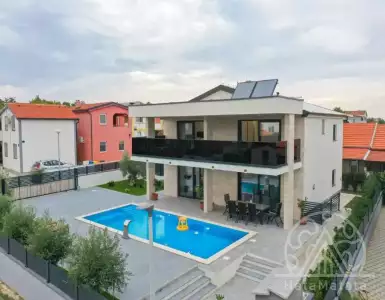
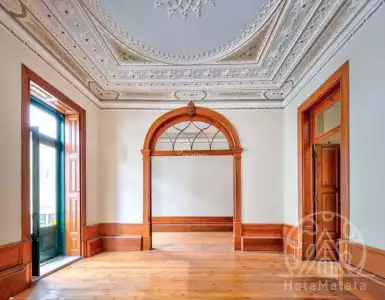
Subscribe to the newsletter from Hatamatata.com!
Subscribe to the newsletter from Hatamatata.com!
I agree to the processing of personal data and confidentiality rules of Hatamatata