The walls of this 3D-printed house, which costs $130,000, were built in 18 hours — take a look inside.
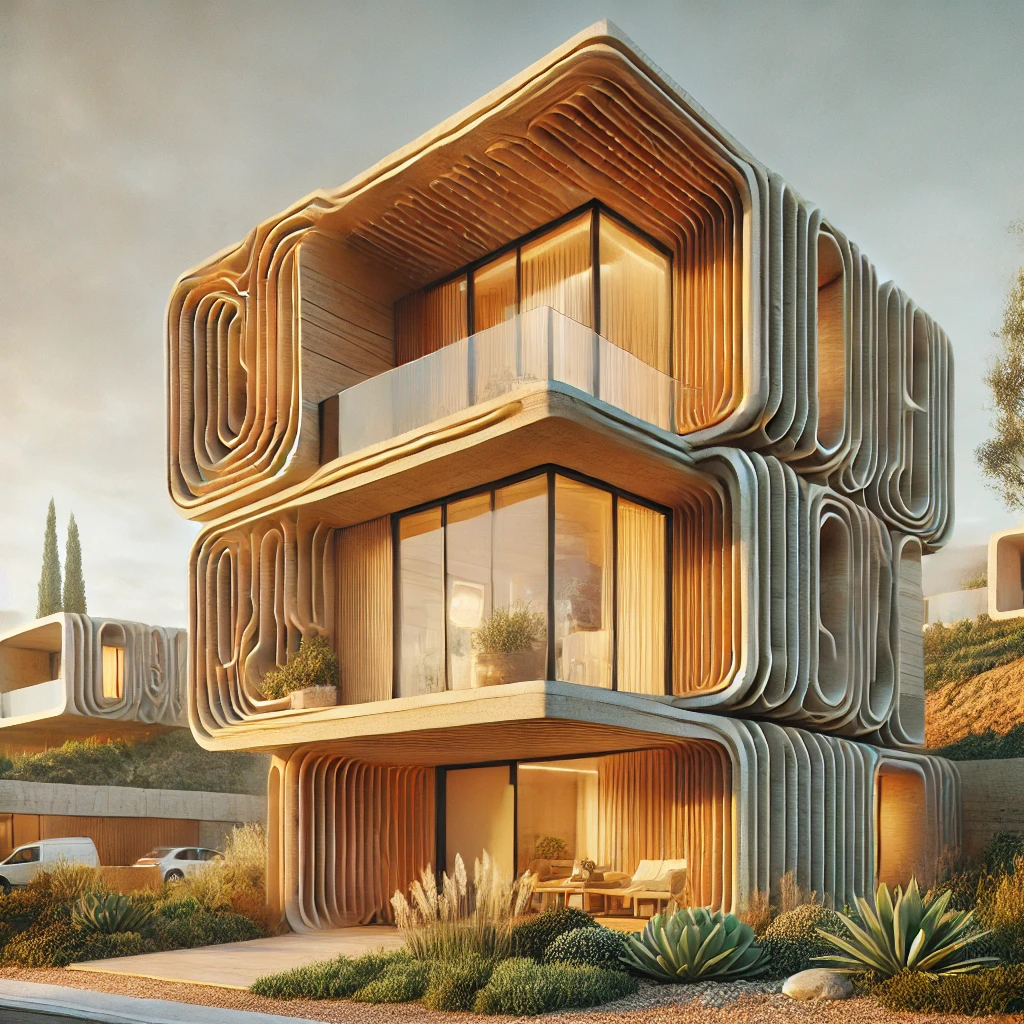
The Portuguese startup Havelar has become a pioneer in the production of the first houses built using 3D printing. Using the flagship printing system from COBOD International, Havelar has completed the construction of its first 3D-printed house in Portugal. The energy-efficient two-bedroom house, covering 80 square meters, was printed in just 18 hours, highlighting the speed of this method compared to the traditional construction industry. Havelar representatives claim that their technology not only accelerates the construction process but also reduces its cost.
If startups like Havelar continue to develop in the same way, the future of affordable housing could look completely different—with perfectly organized "packs of spaghetti" forming strong and functional wall structures. Havelar assures that a custom-built home can be ready in less than two months, significantly below market cost. By integrating robotic printers into the construction process, the company is demonstrating impressive results.
It may seem that such promises sound too good to be true, but the latest Havelar project, which became the first example of 3D-printed housing in the country, confirms their capabilities. The efficiency and speed of printing have significantly reduced costs. Experts note that automated printers, such as the BOD2 from COBOD, enable the creation of quality homes that are resilient to natural disasters, in less time and with lower resource and labor costs.
However, like any new technology, the construction industry using 3D printing faces certain challenges. There are issues such as the high cost of printing materials and a lack of trained specialists. Additionally, modern printers are limited in their capabilities: they can only print walls, and all other elements of the house still need to be completed using traditional methods.
According to one of the founders of COBOD, Philip Lund-Nielsen, by the end of 2023, the company successfully sold over 70 of its "BOD2" printing systems to various organizations around the world. However, despite all the challenges, 3D printing significantly reduces construction time: for instance, the walls of the Havelar house were printed in a record 18 hours.
In the spirit of the recently built luxury home by the American startup Icon in Texas, the contrasting colors and textures of the finishes create a modern and stylish look. However, before you start saving for a down payment, it's worth noting that, as stated by Rodrigo Vilas-Boas, one of the founders of Havelar, their company is interested in partnering with those who want to create sustainable and affordable communities. So far, plans for selling this printed house remain uncertain, as reported by COBOD. Havelar has not commented on these reports, leaving the question of the company's future projects open.
If you dream of affordable housing, it’s worth waiting for the announcement of new initiatives from Havelar. For example, a project is being developed in Texas to create the world's largest neighborhood of printed homes with 100 housing units, which will be completed soon. This highlights the growing interest in modern construction methods. According to Rodrigo Vilas-Boas, with plans to implement new construction methods, including in good neighborhoods, they will be able to ease the first home purchase for those interested, with a potential price of around€150,000which is about$162,000.
For comparison, the prices of the first homes in the new residential complex by Lennar and Icon near Austin range from$476,000to$566,000for a unit. Meanwhile, more expensive homes in the Icon project in Marfa (Texas) start at a price of$900,000and above. Thus, the price differences are quite noticeable, making the models from Havelar more accessible to most potential buyers.
Comment
Popular Posts
Popular Offers
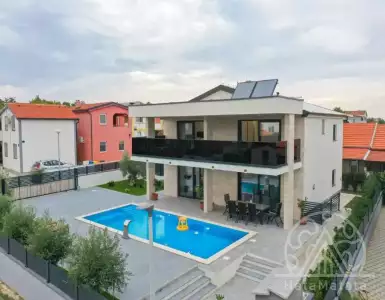
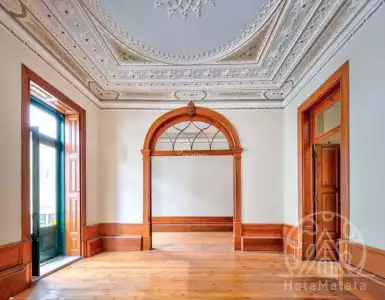
Subscribe to the newsletter from Hatamatata.com!
Subscribe to the newsletter from Hatamatata.com!
I agree to the processing of personal data and confidentiality rules of Hatamatata